At Being Guided I have recently come full circle in my career. I starting out in the plastics industry in 1972 with National Plastics, then the largest injection moulding factory in Europe, established in Walthamstow, East London in 1936.
After training as a mould and product designer, I moved from the plastics industry to the information technology world, initially marketing of pick-and-place robots and getting into the first generation of Computer-Aided Design (CAD) systems for mould design in the early-1980s.
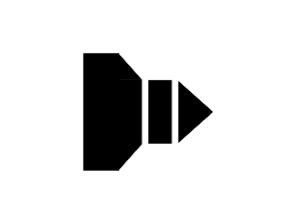
Fast forward 52 years and I am now working with three technology partners to solve compelling problems for injection moulding and mould making firms:
- SIMCON. Simulating part design, mould design and manufacturing tryouts.
- Tangle. Low-code app for make-to-order manufacturing automation.
- Salesforce. Customer Relationship Management (CRM) systems.
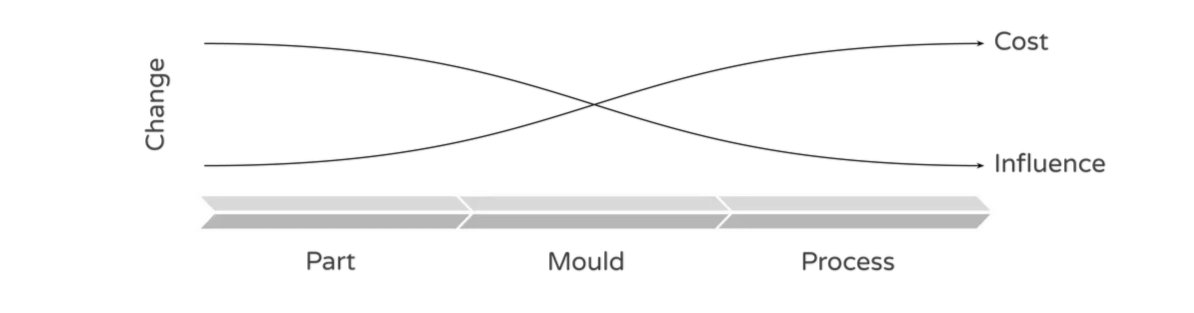
SIMCON Value Engineering
I am creating a new Value Engineering solution with SIMCON, determining the cost of applying (and crucially, the cost of not applying) simulation software at each stage of part, mould and process design.
As illustrated above, SIMCON is all about prevention, not cure. This applies to each stage of the product, mould and process design for injection moulders and mould makers. As you can see, the ability to change decreases and the cost of change increases, both exponentially, as you move through the design and manufacturing stages.
SIMCON simulation software (CADMOULD and VARIMOS) provides a solid foundation for measurably increasing the bootomline performance of an injection moulding or mould making firm. This is where our Value Engineering services are applied. For the owners and senior managers within a plastics injection moulding or mould making firm the key question we answer is this:
What is the cost of NOT buying SIMCON CADMOULD and VARIMOS?
Through a process of Mutual Value Discovery - and supported by our expert partner, Simcon kunststofftechnische Software GmbH, we work with injection moulding and mould making executives to quantify Current State ('As-Is'), without implementing SIMCON and compare this with the financial and other quantifiable gains in a Future State ('To-Be') with this investment made.
This results in the creation of a comprehensive Business Case Calculator.
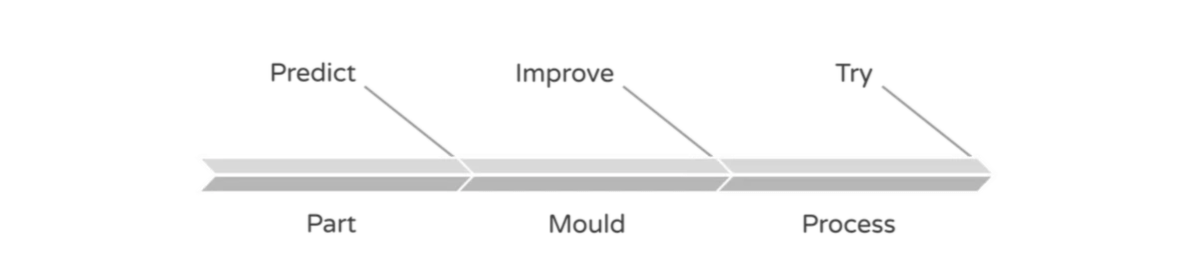
Tangle and Salesforce
I am helping a tech startup called Tangle to deliver its Manufacturing Platform, combined with the world-class Salesforce Lightning Platform. This includes a focus on the UK plastics industry, including the many injection moulding and mould making firms that want to modernise and improve the performance of their operations today.
Salesforce is a world-class Software-as-a-Service (SaaS) platform, best known for Customer Relationship Management (CRM) systems, but offers a broader foundation for many applications, including manufacturing. This is the Salesforce Lightning Platform.
For manufacturing a combination of Salesforce and Tangle Manufacturing provides a coherent combination. This is ideal for make-to-order manufacturing, including specifically the industry reviwed in this blog post: plastics injection moulding and mould design.
The Salesforce Lightning Design System provides the ability to insert Components inside a Salesforce Lightning page. Here we can see that Tangle can become a 'Canvas' within a single page layout. This provides a seamless user experience in one screen.
Tangle Manufacturing is all about the application of a low-code software platform combined with a 'Co-pilot': Open AI's ChatGPT 4. This is Artificial Intelligence (AI) applied to the plastics industry - and specifically, the area of the industry I know very well - injection moulding and mould design.
Tangle Manufacturing makes pragmatic use of ChatGPT 4: AI acting as a Co-pilot to co-write custom software code faster for delivering custom Salesforce and Tangle Manufacturing implementations. This also helps the injection moulding or mould making company to create smarter scheduling.
Consider the real world examples below of problems we solve:
Material and Tooling Optimisation: By introducing SIMCON CADMOULD and VARIMOS simulation software, injection moulding and mould making firms can optimise the each stage of product, mould and process design. SIMCON can suggest the most effective design and related efficient production sequences, including filling, packing, cooling, shrinkage, warpage plus optimised cycle times for manufacturing plastic parts.
Optimised Machine Utilisation: SIMON CADMOULD and VARIMOS similation software can analyse historical production data and current order information to optimise allocation of jobs to machines, ensuring that each machine is used to its fullest potential. This reduces idle times and increases throughput, leading to higher overall equipment effectiveness.
Customisation and Small Batch Efficiency: Salesforce plus Tangle Manufacturing enables smart scheduling to achieve efficient production of customised products or small batches, by intelligently grouping similar jobs and minimising setup times. This allows injection moulding companies to offer a broader range of products without significant losses in efficiency.
Workforce Management: Salesforce plus Tangle Manufacturing delivers smart scheduling to optimise allocation of human resources. This can forecast labour requirements based on production schedules, ensuring that the right number of operators and technicians are available for each shift. This helps in managing labor costs effectively while maintaining high productivity levels.
Quality Control and Compliance: Smart scheduling powered by Salesforce plus Tangle Manufacturing can integrate quality control checkpoints at optimal stages of the production process, ensuring that products meet quality standards without compromising production speed.
Predictive Maintenance Scheduling: By predicting when machines are likely to require maintenance or are at risk of failure, Salesforce plus Tangle Manufacturing can schedule maintenance activities during low-impact periods. This proactive approach minimises unplanned downtime, extends the lifespan of the equipment, and ensures consistent production quality.
Dynamic Adaptation to Demand: Salesforce plus Tangle Manufacturing can adapt production schedules in real-time based on changing demand, supply chain disruptions, or any unexpected machine downtime. This ensures that the company can meet delivery deadlines and maintain high levels of customer satisfaction without over-producing or under-utilising resources.
Energy Consumption Optimisation: Smart scheduling delivered by Salesforce plus Tangle Manufacturing can also optimise energy consumption through scheduling energy-intensive tasks during off-peak hours, when energy costs are lower. This not only reduces operational costs but also supports sustainability goals by minimising the carbon footprint of production processes.